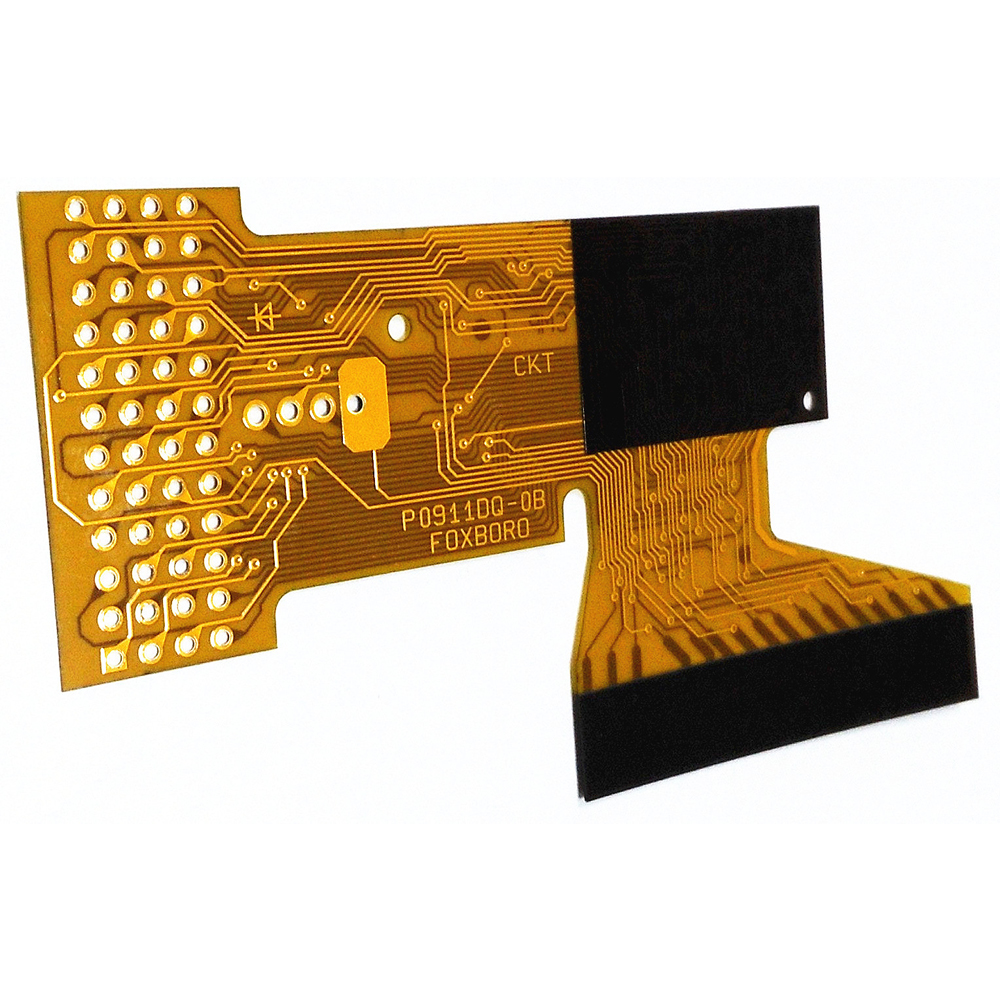


Flexible Printed Circuits Boards
Flexible Printed Circuits Boards made their introduction into the electronics industry as substitutes for cable assemblies. They introduced a number benefits to designers such as reduced weight, reduced size and higher reliability, all at a low cost. As time has passed, the technology has gone through refinement. Today, Flexible PCBs are still used as replacement for cable assemblies, however their scope has evolved to the point of also being able to replace traditional Rigid PCBs. With the ability to mount components based on both SMT and through hole technology, available not only as single sided, but also as double sided THP and Multi-layer technology, flexible PCBs are today utilised in a multitude of applications.
While standard rigid boards have characteristics which make them suited to many applications, the diversity of applications in which electronics is used today has enabled designers to also utilise flexible Printed Circuit Boards as well as hybrid Rigid-Flex Printed Circuit Boards in order to utilise the best PCB technology commercially available for each application.
Today Flexible Printed Circuit Boards are found in the majority of consumer products from computers, where a Flex PCB is used as a cable assembly for hard disk drive heads, to mobile phones, automotive electronics and home entertainment systems just as a starting point.
Advantages of Flexible Printed Circuit Boards:
Higher Reliability for SMT components: Flexible PCBs provide a substantial reduction in strain on component solder joint compared to rigid PCBs. Mechanical fatigue due to thermal stress is a major reliability issue for conventional rigid PCBs. The inherent mechanical properties of Flexible PCBs alleviate this problem, not only making conventional applications more reliable, but being the most viable solution where electronics are subject to a high level of thermal stress.
Reduced size and weight: Flexible PCBs can provide an interconnection density unsurpassed by conventional wire connector technology. Tracking density down to 0.004″ (4Mil) and PCB thickness as low as 0.0005 (0.5Mil), along with the ability to flex, means PCBs can be designed to fit into very small areas and provide a high level of circuit and component density.
Stable Electrical Characteristics: The technology has relatively tight tolerances on laminate thickness and dielectric properties. This enables impedance, cross talk and noise to be accurately determined theoretically and conformity achieved in mass production volumes. Thermal stability ensure conformity over a large temperature range.
Shock and vibration: Flexible Printed Circuit have a low mass and are ductile in nature. These two properties reduce mechanical damage, not only to the PCB, but also to the component solder joints, making them exhibit superior reliability and life in applications which subject the electronic assembly to shock and vibration.
Low Cost: Flexible Printed Circuits enable manufacturing costs to be reduced in a number of ways. Firstly the unit cost of the PCB itself is generally lower than a conventional PCB. Integration of cable assemblies as part of the PCB enables a reduction of parts and labour for the assembly process. This level of integration also allows for the reduction in size of the application product, indirectly reducing manufacturing costs.
Conclusion:
Flexible PCBs provide an option to designers which provide many advantages over conventional rigid PCBs and in some applications are the only viable solution. As electronics become more and more integrated into products which are getting smaller, Flexible PCBs are becoming more and more utilised to overcome the limitation of conventional rigid PCBs.